Woodstock, Epicentre of Cheese Processing for Agropur
For more than 45 years, the Agropur plant in Woodstock, Ontario, has been applying its expertise in cutting, grating, and manufacturing cheese. Let’s visit this large facility that produces 680 million slices of cheese per year.
That’s right: 680 million slices. Placed end to end, they would stretch from Vancouver to Halifax and back … four times! This impressive 82,000-square-foot facility processes 36 million kilograms of cheese each year -- the equivalent of 360 million litres of milk -- for a wide range of customers, from the private brands of major Canadian food retailers to various food service operators.
What makes Woodstock unique is that it is Agropur’s only plant that does not process a single drop of milk. The Cooperative decided to equip itself with a plant specializing in cutting and packaging to meet the high demand of its customers.
Nathan McLaughlin - Plant Manager
Plant manager for the past six years, Nathan McLaughlin is clearly proud of his teams’ efforts to make the Woodstock plant a nerve centre for the Cooperative.
“We’re trying to be the primary knowledge centre for cutting and grating at Agropur,” he says. “We test technologies and monitor what other cheese plants in the Cooperative are doing to optimize our yields and efficiencies.”
As examples, Nathan cites cutting-edge technologies such as the new thermo-forming line, which maximizes the thickness of Swiss cheese to get the most slices per block, and a new cheese holding system that uses suction rather than clamps to reduce waste on the production line. “We want to lead the way, share our knowledge and learn from our Agropur colleagues, our suppliers and other processing plants in North America,” says Nathan.
Improvements That Have Doubled Production
The Woodstock plant, with nearly 300 employees, was the first to implement the Agropur Operating System (AOS) program. AOS has created a dynamic operating environment by setting clear goals and standards and putting people at the centre of the strategy.
Main sources of cheese processed by the Woodstock plant
Notre-Dame-du-Bon-Conseil | White and marble cheddar |
Lethbridge | Swiss and specialty cheeses (e.g. jalapeno Havarti, Monterrey Jack) |
Granby | Pizza mozzarella, cheddar |
Oka | Fine cheeses |
“In 2018, we produced 6 million kilograms of grated cheese, when we only had capacity for 5.7 million kilograms,” McLaughlin recalls. “We installed new tools with AOS to reduce the time it takes to clean the line and make the necessary changes to produce different formats.”
Over the following months, the grating line’s capacity increased to 9 million kilograms. The plant copied the gains to other processing lines. Overall, the plant’s processed cheese volume increased from 17.5 million kilograms to 36.2 million kilograms. Several factors contributed to the increased volume, but Nathan McLaughlin believes the AOS program made the biggest difference.
“The principle behind AOS is to focus on waste and downturns,” says Nathan. “By removing obstacles and helping teams build their capacity, we help improve the operator experience and enable them to concentrate on more proactive activities that add more value to the business.”
According to Nathan, who sees his role as plant manager as a leader serving his people, AOS provided the tools to achieve this phenomenal increase in production. “Our fantastic team worked hard to integrate the new system to generate and manage this growth. The demand for sliced and grated cheese in the marketplace is high, and thanks to AOS, we had the capacity and volume to meet it.”
Day-to-day Agropur Values
The performance speak for Woodstock’s success: The plant saw a 44% reduction in operating costs over six years and an 84% drop in emergency response calls over the same period, as well as a 65% reduction in customer complaints over four years.
The Woodstock team truly embodies Agropur’s values, as evidenced by the excellent results and the boldness shown by the entire team in embracing change and overcoming challenges. Communication with other plants in the organization is also a daily practice at the plant. “We are customer-oriented and constantly improving the quality and performance of our products. It’s a win-win collaboration with them,” concludes Nathan McLaughlin.
Look for the code 1555 on your products. It will confirm that the cheese was packaged at our Woodstock plant.
YOUNG LEADERS
Young Cooperative Leaders Program
Agropur’s Young Cooperative Leaders Program celebrated its 40th anniversary in 2022. Participant Patrick LeBlanc tells us about the program as registration opens for the latest cohort.
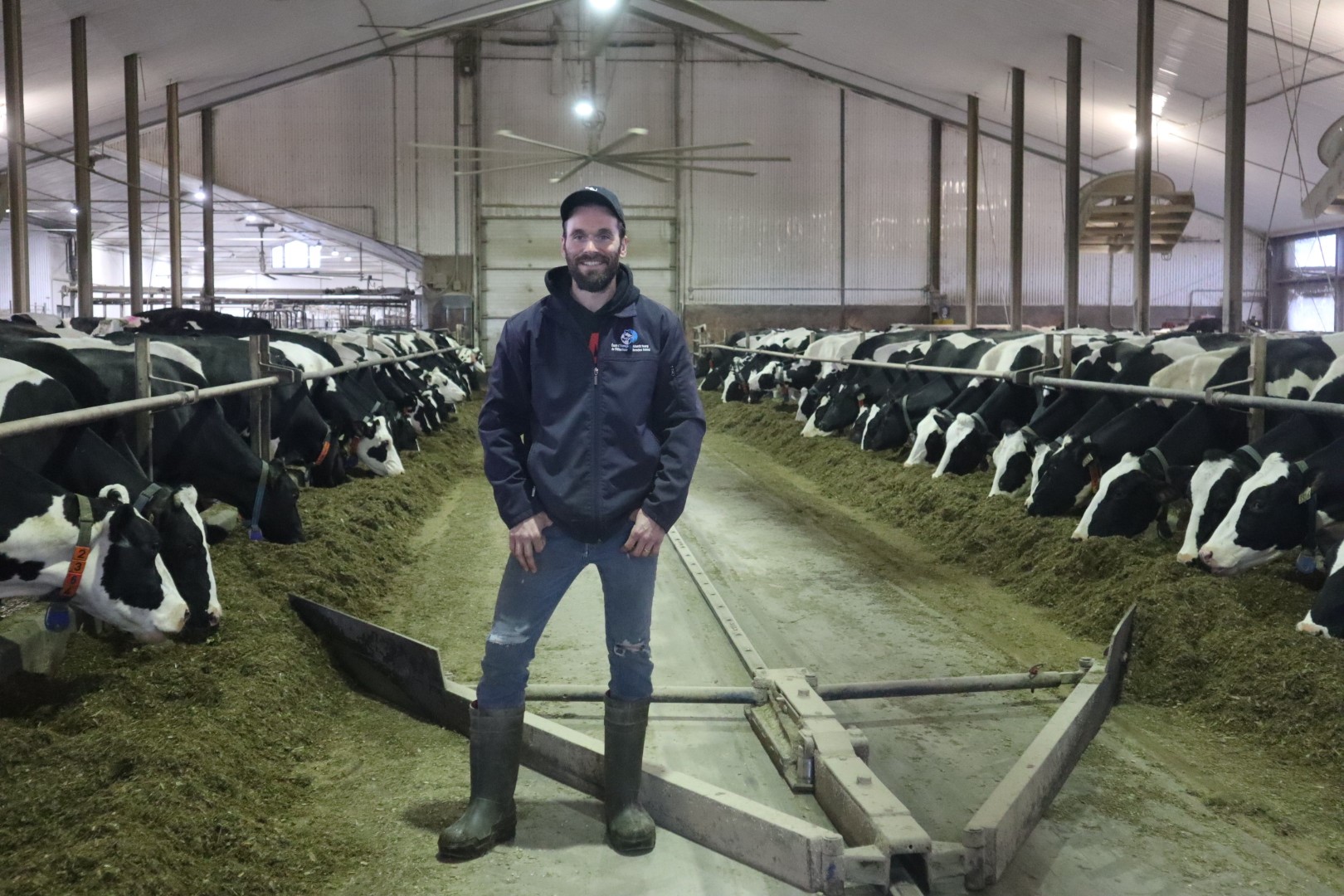